It is significantly more difficult and costly to remove contaminants from machinery than it is to modify and protect equipment against contaminant ingression. Especially in turbine applications with a large volume of oil, keeping possible contamination sources away from lubricated equipment and performing routine flushings are your best lines of defense. Contaminant exclusion revolves around modifying equipment to protect against solid particles, water, and other contaminants that are trying to enter your machines, thereby avoiding costly repairs and machine downtime.
The Risks of Contamination
When machine parts and the lubricant protecting the machine’s internal surfaces are exposed to contamination, it is like pouring gasoline on a lit fire. The lubricants that should be protecting metal surfaces are now having to fight against contamination. Additives meant to emulsify water, envelope particles, disperse foam, and even improve the lubricant’s viscosity index are now in overdrive trying to compensate for the additional harm caused by incoming contaminants. In turbine applications, the depletion of important additives can cause varnish and sludge to build up much faster as the oil oxidizes, degrades, and ultimately damages equipment.
Solid Contamination
Solid contaminants include byproducts from the machine’s environment such as dirt, dust, and metal from internal machine wear, and they can cause serious damage to your machines and lubrications. Solid contaminants enter your machine parts and reservoirs through a variety of pathways. These pathways include mechanical wear, corrosion, oil degradation, and invasive inspection and repair activities. They can even exist in new machine parts coming from the factory.
A primary source of contaminants is the inhalation of airborne contaminants into the reservoirs and tanks. The forced convection of air through thermal siphoning, machine-driven air currents (gear movement), and cyclical changes in the tank oil level can escalate contaminant ingress. The air enters through vents and breathers and moves past machinery parts such as shaft seals, unsealed hatches, and other unprotected machine openings. In this way, contaminants are carried throughout different machine components and jeopardize the entire machine.
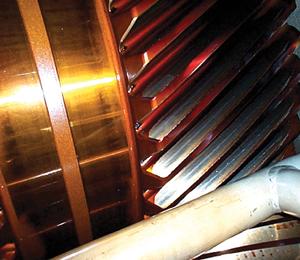
Despite this, solid contamination is easily preventable with testing, modification implementation, proper flushing, and enhanced training. By analyzing the particles found in used filters or the sump sediment, you can create an accurate picture of what contaminants have gotten into your machines and how they got in. From there, you can begin including more contaminant exclusion practices into your routines such as retrofitting hardware and performing routine maintenance tactics to stop contaminants from entering.
Routine maintenance tactics to start implementing include installing proper breathers on machine and lubricant storage vessels, improving seals, having tighter system closures, and taking greater care during internal inspections and part replacement processes. To help prevent solid contamination during part replacement, you should always properly flush the equipment before installation, during the commissioning process, and again shortly after the first start-up. This ensures that any remaining contaminants won’t be able to gain access to your machinery and lubrication. Metal contaminants produced during manufacturing can also become stuck inside the reservoir housing, gears, and bearings. Flushing the reservoir helps remove any large metal fragments that may become trapped.
It is important to remember that your machinery requires you to be proactive in investing in its reliability and overall wellness. The cost of excluding a gram of dirt is only 10 percent of what it will cost once the dirt gets into your oil.
Water Contamination
The most common lubricant and machine contaminant is water. Water is used throughout the manufacturing process, especially condensation, and can be found in the environment in the form of rain or humidity. When you mix water with heat, air, and metal, the oil will begin to oxidize and destroy the lubricant and equipment.
How to Detect Water Buildup
One way to monitor equipment from water buildup is with a bottom sediment and water bowl (BS&W bowl). This clear sight glass allows you to visually inspect the reservoir or sump and lets you drain off any water or sludge that may have accumulated. These are especially helpful on large reservoirs that use an oil cooling system. Coolant systems will start rusting from the inside and will start leaking into the oil reservoir, contaminating the oil. A BS&W bowl allows you to quickly catch the leak before it becomes catastrophic.
Managing and Eliminating Water Contamination
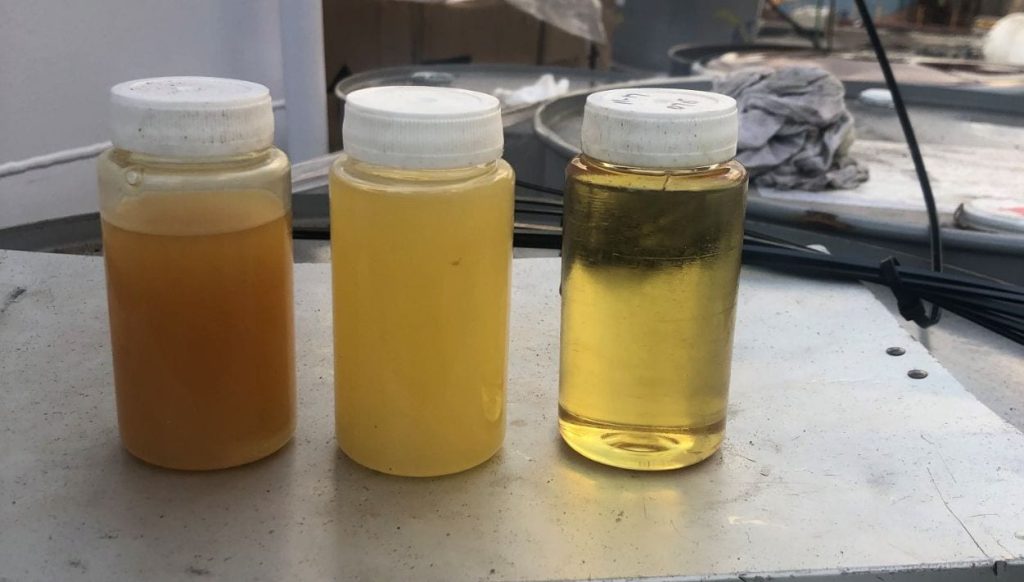
Measures you can take to keep water out of your systems include training your staff, performing routine leak inspections, building barricades, and making sure all equipment seals and gaskets are fresh and on correctly. Also, try to exclude all water contact with machine parts except for necessary washdowns. Performing washdowns on machine parts can be tricky. You want to keep your equipment clean without contaminating the lubricant in the process. Training and machine guarding are the best lines of defense.
Condensation is also frequently overlooked. Left unchecked, it’s a silent killer to your equipment. Condensation in machinery is caused when hot, humid ail cools down and forms water drops on interior surfaces and slide into the oil. A BS&W bowl can be a lifesaver in these instances because it gives you an indication if there is excessive water present. Some machines in high-humidity areas would also benefit from having desiccant breathers installed to prevent airborne water contaminants from entering.
If condensation is uncontrollable, using a filter with water capturing capabilities is a great alternative. Filters and dehydrators can be used for removing water from the oil in the system. Otherwise, the water inside the system is likely to cause damage. Eliminating the contamination problem before it enters the system is always cheaper than having to remove it, so focus on exclusion first and use removal techniques only if moisture cannot be prevented.