Amidst all the various components in a plant, small reservoirs often go neglected. Larger equipment tends to be deemed critical due to being high-dollar items. Smaller equipment only gets noticed when it holds up production. Reliability goals with larger equipment is usually pretty straight forward; prevent outages and increase production. Longevity of the equipment is a byproduct of our ultimate production goal, so why is this so often forgotten when it comes to the smaller stuff?
For equipment with reservoir capacities of just a few ounces to 10 gallons, a simple oil level check can be the difference between premature equipment failure and adding up to 10 more years onto its lifespan. Top up reservoirs with low oil levels — seems easy enough, but if each employee has a different manner of performing this task, the lack of consistency becomes a breeding ground for human-induced mistakes which can grow into real headaches later.
Bad Practice vs Best Practice
Regardless of whether you are topping off a gearbox, pump or other oiled component, here’s what to avoid and how to correct some of those bad habits. Some practices are easier to turn around than others. Keep in mind that those that require more planning, investment and time to bring up to speed with best practice will save you from going down that dark road of machine failure.
Funnels
Funnels are extremely popular for obvious reasons. They’re everywhere and anywhere in any given plant. But therein lies the problem. Funnels sit around in lockers or in the back of utility vehicles and collect dust and debris.
Oftentimes funnels are drip-dried and thrown about until somebody else needs to use one. Then that person will pull out a funnel to top off a reservoir and may or may not wipe it off before pouring oil through it. Any dirt that has accumulated onto that funnel will be transferred into the reservoir.
Best practice would be to clean the inside and outside of the funnel with a lint-free cloth. After you’ve used the funnel, clean it again. Store it in a new zip-close bag, seal it and return it to its permanent location. Or better yet, use single-use funnels. You must agree on a permanent spot for funnels to go. This will save you much confusion and frustration in the future.
Open and Galvanized Containers
Unsealed oil-transfer containers might be your only way of transferring oil at your plant. Not uncommon, but we must realize that the container’s openness is its downfall regarding contamination. Any particles, large or small, entering a sump from an open transfer container will eventually become scattered into microscopic pieces throughout the machine, causing havoc. Remember, the particles between 3-10 microns do the most damage in our equipment.
Galvanized pails also have a zinc coating to protect the steel from corrosion. This coating unfortunately has a habit of attracting oil additives to it. The oil you pour into the reservoir will have been stripped of these additives, and you’ll be none the wiser.
Best practice would be to do an inventory check and throw all open and galvanized containers away. You should purchase sealable and reusable containers and transition your team into using them. If you supply your team with the right tools, good practices will follow.
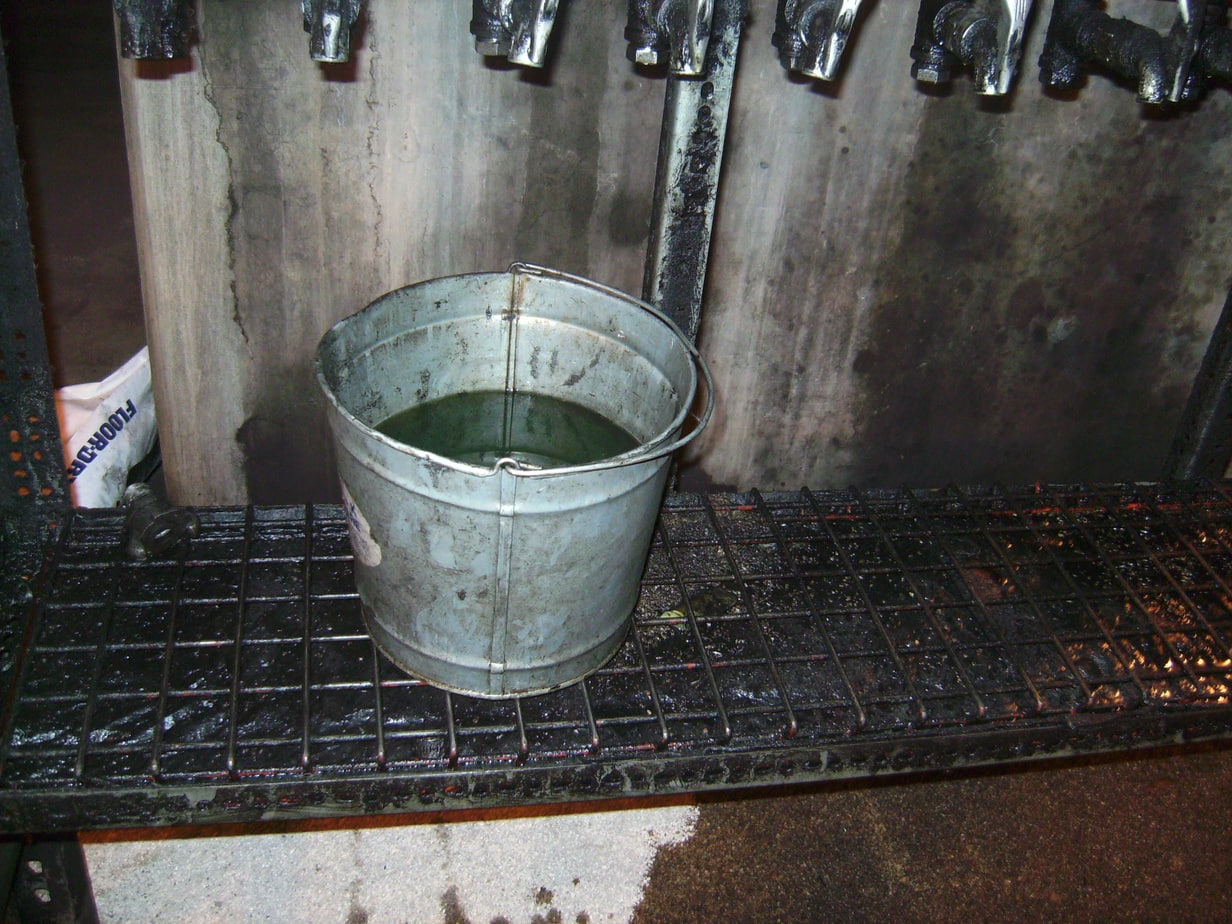
Sealable and Reusable Containers
Sealable and reusable (S&R) containers can be a nearly perfect solution for the ills caused by open and galvanized containers, but you must still be mindful not to leave them in the field next to equipment and to keep any spouts closed until it is time to pour. Cleanliness and correct labeling is also of the utmost importance here.
Best practice would be putting a PM in place to thoroughly clean the inside and outside of the containers with a lint-free cloth. Cleaning should take place inside of a clean room to prevent any contamination. IFM’s veteran lubrication technicians can assist your organization in establishing a spotless and well-documented lube room with all necessary labeling.
Cleaning Before Filling
Be aware of how debris settles on and around fill ports. If not cleaned, contamination is ready to pounce the second that port is opened. A small amount of dirt falling in would still mean wear particles running wild inside your machine and can even lead to component failure. Best practice would be always bringing rags or wipes with you into the field and cleaning fill ports before opening them.
Dirty Oil
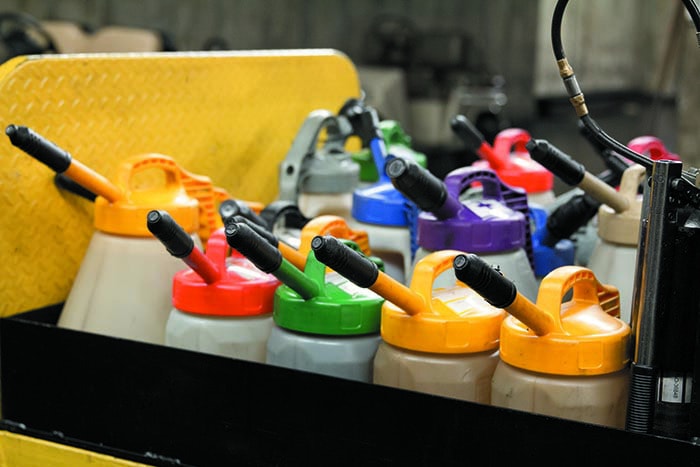
You may think that new oil is always clean oil, but this isn’t always the case. Keep in mind that every time that an oil is transferred, we are creating another opportunity for that oil to get even dirtier.
Best practice would see all oil entering a facility go through a decontamination process before being introduced to any machines. Define target cleanliness levels for all equipment, even if oil analysis isn’t going to be performed. You’ll only be able to hit optimum equipment reliability if your new oil meets these target specifications.
Fill it and Forget It
This mentality of putting a piece of equipment into operation and never looking back must go. Seals wear and leak. Plugs loosen over time. Small bath systems depend on correct oil levels. All machinery needs to be examined at some point. Simple daily or weekly inspections should be performed on all assets. A slight fluctuation in oil level negatively impacts the internal components in most small reservoirs. Putting PMs and routine inspections in place is necessary to make servicing forgettable equipment standard practice.
Contamination Control
Controlling environmental elements goes hand in hand with more traditional contamination control practices. Headspace management must be a key focus. If you are located somewhere humid, wash down applications and outdoor equipment. Consider implementing desiccant breathers, for example. Ensure that the micron rating of any breather you select will provide necessary protection.
Training
Without proper training, all this advice is meaningless. The same bad practices will repeat in a vicious cycle unless you take the steps to fix the work mentality and knowledge gaps within your team. Even if your plant swings closer to the bad practices than the best, you are already one step closer to improvement by simply acknowledging your faults.
It isn’t fair to put your team to task without arming them with the right tools. We rely on certified electricians for electrical work, certified welders for welding jobs, and you even have to be certified to operate a fork-truck… maybe it’s time to re-evaluate the way we manage lubrication and consider seeking help from certified lubrication technicians. Proper training now by experienced experts can ensure that your facility has a bright future with increased efficiency and decreased production hold ups.