Unfortunately, for many operations, high velocity oil flushing is just another item on a checklist, done without much thought or planning. For facilities like this, the only time oil flushing is a priority is when a system fails, and at that point, the only goal is to get the system back up and running. While this approach is understandable, it often leads to problems, inefficiency, and a cycle of reactive maintenance activity.
Performing high velocity oil flushes at regular intervals can enhance machine performance and extend asset life.
Commissioning / Modifications
During commissioning or after a modification of a machine it is common to find all types of debris. Turbines, compressors, or hydraulic oil systems can all experience catastrophic consequences if an oil flush is skipped during commissioning or after a major machine modification has been made.
Reactive Oil Flushing
After an inspection, breakdown, or repair is one of the most common times for an oil flush. In most instances, that means the project is a reaction to some problem that has been detected. In this case, getting the job done safely, without leaks or spills, and at a high level of quality are the primary concerns.
Contaminants from breakdowns are usually spread throughout the system unless it has been designed with oil flushing in mind. Although some contaminants may be removed by an in-line return filter and some settle in the reservoir, the whole system must be flushed.
In a properly designed system, contaminants from pumps or motor failures may be restricted to a certain part of the system by in-line filters. In these cases, you can flush the reservoir, piping and components within the contaminated area without needing to flush the whole system. This is just one simple example of the work and time that could be saved when a system is set up proactively with flushing in mind.
Preventative Oil Flushing
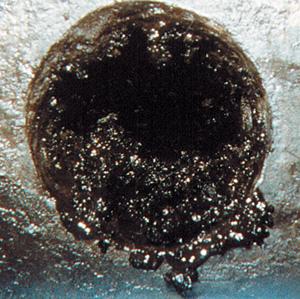
If you are using a preventive approach, it is important to plan work to minimize the external contaminants entering the system. Use proper coverings as soon as possible until the system is assembled and sealed.
If yours is an older system design that collects contaminants in the reservoir or a low fluid velocity allows contaminants to settle in piping, flushing is especially important. Unless you are flushing often enough, a layer of contaminants could easily break free one day and cause a catastrophic breakdown or failure.
Even after a preventative flush, it is important that the system run without a full load (unpressurized) until the contamination level is confirmed to be within acceptable limits.
Proactive Flushing
Taking a proactive approach to flushing, where the procedure is performed often enough to maintain a target high level of cleanliness, is an excellent way to maintain highly critical machines.
In some cases, it is more cost-efficient to perform proactive flushing than it would be to implement a costly upgrade or modification to solve contamination accumulation problems.
Following a Clear Process
The process of high velocity oil flushing is complex and must be done correctly; improper flushing techniques can damage equipment. Because most maintenance personnel are not qualified to perform a proper oil flush, it is a task best left to experts. Good oil flushing companies should have references and case studies as evidence of the success of their process. Gaubert provides these and works with onsite personnel to ensure that the high velocity oil flush is turn-key and aligned to the specific machinery. A proper high velocity oil flush will involve the following steps:
Planning the Oil Flush
This stage, which is hopefully done while a machine is still up and running and not after it has already failed, involves creating a customized approach to the flushing process. A written procedure will be created, outlining in detail the steps that will be taken, the equipment that will be used, the components that will be bypassed, safety and cleanliness requirements, and other important information. The creation of a flushing plan should be a joint effort, with both the flushing service company and the client having input.
Pre-Flush
Before the actual high velocity oil flush is performed, equipment like jumpers must be installed, components that cannot handle the flush must be removed, and a visual inspection of the entire project must be performed to ensure the system is ready for the flush. This inspection specifically looks for leaks and other issues that may arise once the flushing circulation process has begun.
Planning the Oil Flush
This stage, which is hopefully done while a machine is still up and running and not after it has already failed, involves creating a customized approach to the flushing process. A written procedure will be created, outlining in detail the steps that will be taken, the equipment that will be used, the components that will be bypassed, safety and cleanliness requirements, and other important information. The creation of a flushing plan should be a joint effort, with both the flushing service company and the client having input.
Execution
Once everything is in place and the equipment has cleared inspection, the flush begins. For a high-velocity flush, highly turbulent oil is forced through the machine, and other methods like vibrators, mechanically knocking pipes, and hot and cold oil cycles may be used depending on the circumstances. During this stage of the flushing process, a confined space cleaning may also be performed, wherein technicians enter and manually clean parts of the system.
Once the high velocity oil flush has been executed, a visual inspection and a patch test are performed, ensuring that the oil and machinery have been cleaned to the standards set in the planning process.
Documentation
Once everything is in place and the equipment has cleared inspection, the flush begins. For a high-velocity flush, highly turbulent oil is forced through the machine, and other methods like vibrators, mechanically knocking pipes, and hot and cold oil cycles may be used depending on thecircumstances. During this stage of the flushing process, a confined space cleaning may also be performed, wherein technicians enter and manually clean parts of the system.
Once the high velocity oil flush has been executed, a visual inspection and a patch test are performed, ensuring that the oil and machinery have been cleaned to the standards set in the planning process.
Communication
Throughout the process, frequent and clear communication is critical to success. Be sure your supplier has a plan to communicate with you frequently about the status of the project and any changes to timeline, scope or cost.
Free Whitepaper Download
Getting out of the cycle of reactive maintenance can be difficult, but turning to experienced partners in lubrication can help you uncover ways to be more efficient, proactive, and successful in your maintenance and reliability efforts. Oil flushing is just one way among many that IFM technicians and service teams can help you manage and optimize lubrication efforts at your plant.