Turbine engines have different demands than other engines; they have unique structures, operating cycles, operating temperatures, and contamination potential. As such, turbine engines require unique lubricants formulated specifically to meet these demands.
It is important, when choosing a turbine oil, to understand how these lubricants differ, physically and chemically, from other lubricants. The lubricant selection process is also a good time to address turbine oil system flushing and the initial filtration requirements.
When choosing a lubricant, performance and lifespan are usually top-of-mind. And with some turbine sumps having a capacity of 1,000 to 20,000 gallons, there are clear incentives for long-lasting lubricating oils. The factors that impact a lubricant’s lifespan: heat, contamination, water, aeration, operating hours, etc., can all be managed and referred to when determining which lubricant to choose; but to truly extend a lubricant’s lifespan and to get the most out of it, proper machine maintenance and contamination control, including high velocity oil flushing, are the best tools to use.
Performance Characteristics of Turbine Oils
Most turbines (steam, gas, and hydro) utilize rust and oxidation inhibiting oils (R&O oils). These lubricants, as their name suggests, are intended to hinder the oxidation process — the aim being oxidation stability. R&O oils facilitate oxidation stability by implementing antioxidants, rust inhibitors, and demulsibility additives.
Because, unlike common gasoline and diesel engines, most turbine lubricants are not exposed to soot or fuel, they generally don’t need to be drained and replaced as frequently. Instead, turbine lubricants are designed to shed water and allow particles to settle for easier removal, either through sump drains or kidney loop filtration.
The agents of oxidation, which, again, include water, heat, particulate contamination, and aeration, cannot be stopped by oil additives alone. Other tools like filters, oil coolers, and water removal systems are also effective in the fight against contamination and oxidation.
Turbine System Flushing
Different methods of flushing serve different purposes. If a drain and fill procedure is performed, a displacement flush is likely sufficient. For instances that require more vigorous flushing, such as initial turbine oil fills, periodic maintenance, and thorough system cleanings, a high velocity oil flush should be considered.
A high velocity oil flushing procedure mechanically cleans the inner surfaces of oil systems. The process involves forcing oil (which is often heated to reduce viscosity) through the machine’s pipes at high speed; doing so creates a turbulent flow in the oil, which dislodges varnish and other debris from the pipe surfaces. The oil then carries this debris to the system’s sump, where it is removed. Manual cleaning of the sump is also often performed.
A high velocity oil flush procedure performed by IFM is a carefully planned and implemented operation; every step of the process is documented and reported. Mechanical engineers create a flush design and determine a flow path, and jumpers are used to bypass any critical components that cannot handle the pressure of the flush. Inspections are performed before and after the flush, and cleanliness is verified before the job is considered complete.
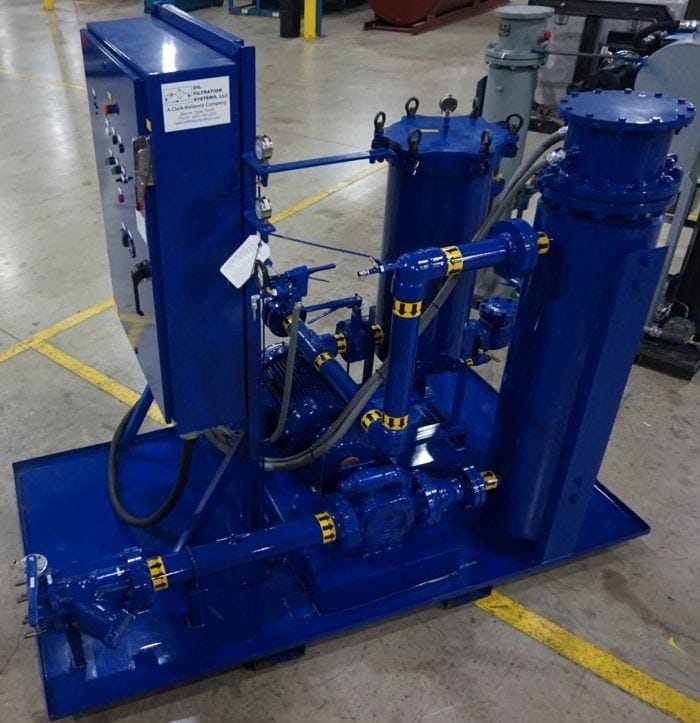
The Benefits of High Velocity Oil Flushing
Cleaning a machine’s lubrication system with turbulent oil offers many benefits, including:
- Reduced wear of lubricated parts
- Longer times between repairs
- Reduced filter consumption
- Long-term system and oil purity
- Increased oil durability
- Reduced total operating costs
Dirty Oil Systems: A Major Problem
The problems associated with dirty oil systems are typically underestimated, often with expensive results. A dirty oil system leads to dirty oil — the root cause of most machine reliability problems, including premature wear and equipment breakdown.
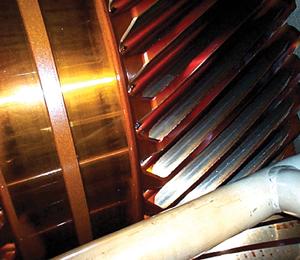
Impurities and contamination can enter a machine (during assembly, during repairs, or from the machine’s operating environment), or they can be created within the machine through oil degradation and corrosion processes. Some of these impurities can accumulate on the walls of the machine’s lubrication system, creating deposits and buildup.
A high velocity oil flush creates a clean system, but efforts must be taken to maintain it. The implementation of a proactive lubrication program is the best way to facilitate continued cleanliness and operational efficiency.